
The Prototype
Once the final design was decided upon. Then it was time to start building the prototype. The only thing still unclear was the choice of material for the handle.
There were several possible materials and processes to manufacture a handle for our participant:
There are two basic types of foam. Flexible foams have an open cell structure and can be produced in both high and low densities. Applications include cushioning for furniture and automobiles, mattresses and pillows, automotive trim, and shoe soling. Rigid foams (ones that we use during workshops) are highly cross-linked polymers with a closed cell structure that prevents gas movement. Their main application is as insulation for buildings, refrigerators and freezers and refrigerated transport vehicles.
It seemded like production of flexible foams won't be possible with our capabilities. Molding flexible foams (rubber foam included) requires a lot of chemicals. Moreover, used chemicals when trigger heat generating chemical reaction which can be quite dangerous. Therefore we decided that form flexible foam in a desired shape was not a suitable option for building our prototype. We asked for advice from the workshop employees about what else we could use to shape flexible foams. Although it seems like it will be quite challenging, this is a possible option.However, we wanted to use a type of foam, because it would be quite comfortable for the user to hold. We therefore decided that we should use already existing foam, that we retrieved from the workshop.
Building the handle
The handle was designed with a soft foam wrapped in leather to make the grip as soft as possible. The leather, seen in the final prototype at the end of the page, protects the foam from sweat and is easily cleanable if it gets dirty as a result of food, drink, or other contamination. The core of the handle is from wood to give it some weight as our participant indicated a preference for.
During one of the three workshop sessions, our projectgroup was working on building a prototype. The choice of material was based on te softed foam in the wrokshop.
In Figure 1, the foam is taped to the wooden base. In Figure 2, it can be seen that the retractable cord is attached to the the handle.
In figure 3 it is clear that the handle is retractable via the retractable cord.
Figure 5 displays the way that the user is supposed to hold the handle.
Attachment system

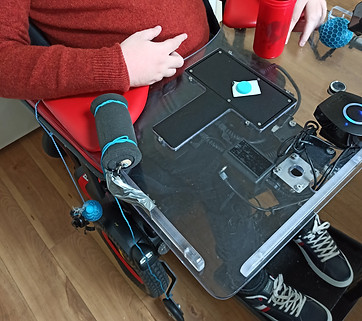
For the attachment mechanism, a few options were considered namely: tape, magnets, velcro, screws, and some sort of clamp. The requirements for the attaching mechanism are that it shouldn't damage the desk of our participant and that it shouldn't get in the way of our participants day-to-day life. This means that it should either be removable or on a part of his desk that isn't used daily for other activities. With these requirements in mind, the clamp was chosen as the best option. The clamp is designed to fit snugly around the participant's desk, sliding on from the side. In the left image you can see how a bolt is used to clamp the prototype to the desk. The form was made as small as possible, in order to make it minimally obstructive. The set-up can be seen in the image above.
Retractable cord
The retractable cord was taken from a retractable badge holder. This cord is placed inside the 3D printed clamp as can be seen on the right. This would give the handle a stable position. The cord is attached to the handle with a screw through a metal ring into the wooden center. The retractable cord is used in order to provide tension, affecting and ideally reducing the participant's tendency to raise his hands to face level. Additionally, the fact that the handle always retracts to the same position means that it does not fall off the desk, which was a problem that was observed in the previous iteration that used stress balls.
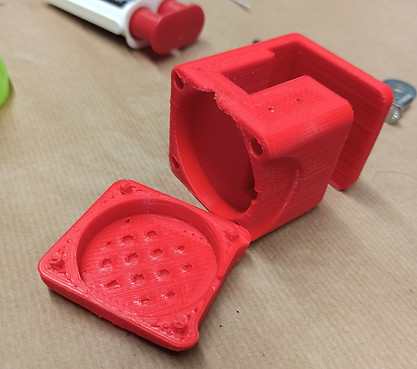
Flic button
The last part of the prototype is the flic button. This is placed on top of the clamp to reduce the space used on the participant's desk and to integrate it with the other part of the concept.


Final Prototype
For our finalised prototype we put everything together as can be seen on the pictures below. The concept is all finished in a nice red and black theme. The partcipant wanted the product to match his wheelchair.


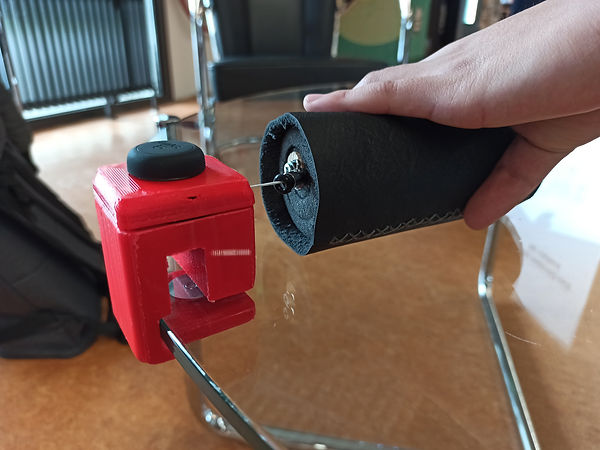
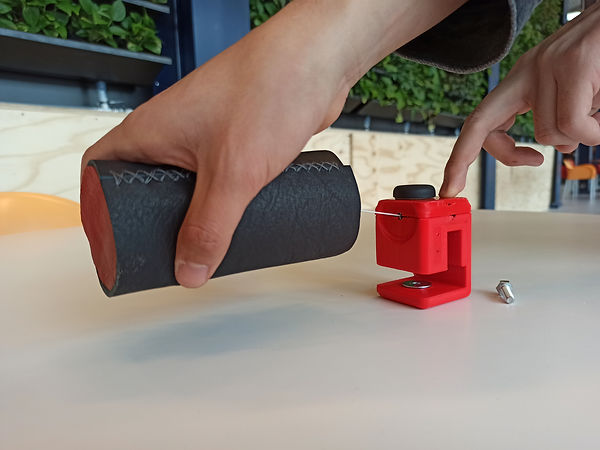